¿Qué es Alucobond y cómo instalarlo?
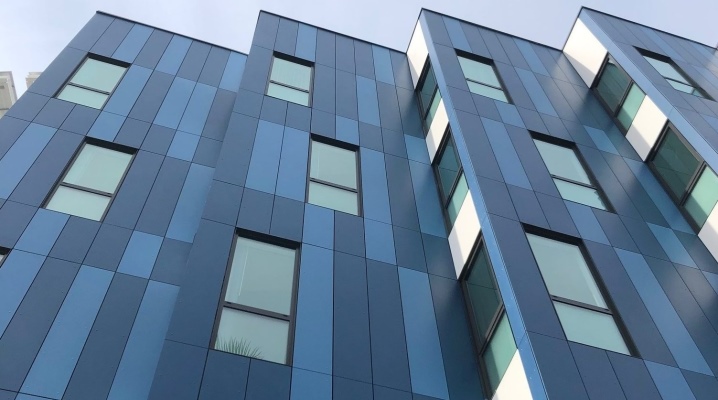
El material para la decoración de fachadas llamado alucobond gana cada año una gran popularidad en todos los continentes. Hay varias razones para esto. En primer lugar, es un costo aceptable. Luego viene la belleza externa de las losas. Y, sin duda, la alta calidad es una característica positiva. Los artesanos también aprecian este material por su facilidad de instalación. Sin embargo, antes de continuar con la instalación independiente del alucobond en la fachada de su propia casa, se recomienda conocer las propiedades de este material, las ventajas, desventajas y también familiarizarse con algunos de los matices de la instalación.
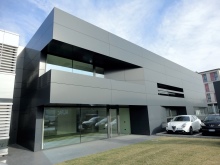
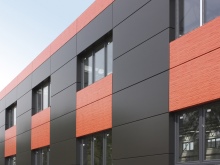
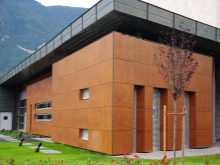
¿Lo que es?
Alucobond es un material compuesto cuyo nombre completo suena a paneles compuestos de aluminio. En este caso, el composite es un dúo armonioso de aluminio y polímero. El polímero utilizado en la fabricación de bloques compuestos difiere en tipo y grosor. Las características de rendimiento del material acabado dependen de esto.
Solo en el territorio de la Federación de Rusia, hay alrededor de 15 empresas dedicadas a la fabricación de este material de revestimiento.
El espesor de las láminas de aluminio utilizadas en cada placa es de 0,5 mm. El relleno interior de los bloques se envuelve con placas de metal en ambos lados. Así, se forma una especie de sándwich.
El componente interno de dicho sándwich se presenta con mayor frecuencia en forma de polietileno de alta presión.
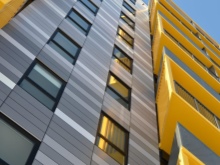

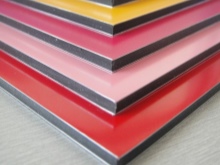
Es importante saber que las láminas sándwich de aluminio tienen un recubrimiento anticorrosión para asegurar que las tablas no se deterioren prematuramente. Además, El revestimiento anticorrosión ayuda a evitar daños por roce contra la base de la celosía. Como capa anticorrosión se utiliza una composición de óxido en forma de solución de hidróxido de sodio, por lo que aparece una película en la superficie de la placa de metal, que protege el material de la humedad que puede causar un daño irreparable al metal.
El anverso es de aluminio recubierto de poliéster. Sin embargo, los fabricantes utilizan con mayor frecuencia carbón fluorado, que no está expuesto a la radiación ultravioleta ni a los productos químicos. Lo que es digno de mención es que el carbono fluorado, incluso después de un funcionamiento prolongado de las placas, no se agrieta y, más aún, no se aleja de la base.
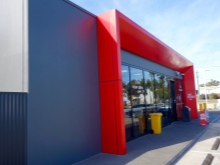
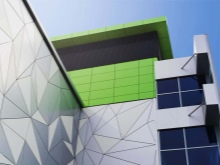
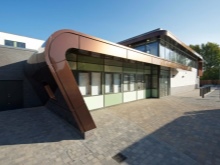
La capa final del sándwich compuesto es una película laminada. Debe retirarse antes de la instalación, ya que forma parte del embalaje original. Gracias a esta película, la superficie decorativa de las losas está protegida durante el transporte y la manipulación. Algunos artesanos instalan paneles compuestos de aluminio sin quitar la película y luego quitan la capa protectora de la superficie.
La parte frontal de las placas de alucobond se distingue por una gran cantidad de capas. Cuando se ve desde el relleno central, la siguiente capa es la adhesión, luego la lámina de aluminio, luego la imprimación, la resina, el esmalte y la película protectora.
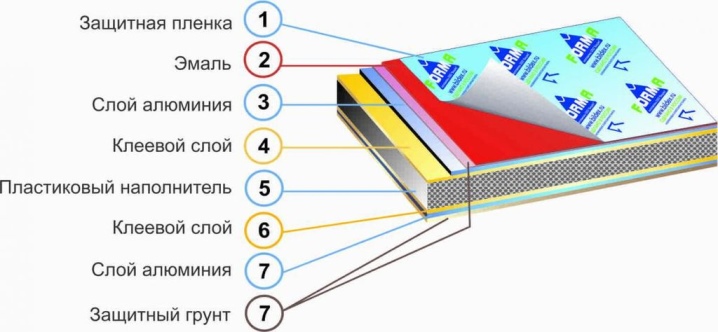
Características principales
Alucobond es un material de construcción de revestimiento en forma de bloques compuestos de aluminio. Debido a su contenido, los tableros tienen buenas características de desempeño.
Además, se propone familiarizarse con las ventajas y desventajas de alucobond, que toda persona que quiera utilizar este material como revestimiento de la fachada de un edificio debe conocer. En primer lugar, debe conocer los beneficios de los tableros compuestos.
- Durabilidad. Cada fabricante proporciona un certificado de calidad y una tarjeta de garantía, confirmando que los paneles durarán hasta 25 años. Sin embargo, los propietarios, que han utilizado este material hace mucho tiempo, afirman que las losas de alta calidad de empresas conocidas pueden durar medio siglo.
- Facilidad de procesamiento. A pesar de las múltiples capas, los paneles compuestos son bastante fáciles de cortar en varias piezas. Se alimentan mediante laminación y soldadura.
- Fuerza y elasticidad. Las planchas de acero en sándwich de material compuesto confieren a los tableros una alta resistencia a cualquier esfuerzo mecánico. Pero lo que es interesante, a pesar de la presencia de un material tan fuerte, el alucobond se puede doblar.
- Resistente a la intemperie. El revestimiento de alucobond es capaz de resistir las inclemencias del tiempo y los cambios bruscos de temperatura.
- Estética. Gracias a una amplia variedad de colores y matices del anverso de las placas de alucobond, todo el mundo podrá plasmar las ideas más atrevidas en la realidad. El exterior puede imitar el enlucido decorativo y otras opciones de diseño únicas. Y lo que es más agradable, incluso con una exposición prolongada a la radiación ultravioleta, la saturación de color de la parte frontal de las placas no desaparece.
- Superficie lisa y plana. Incluso cuando las losas están dobladas, no aparecen grietas ni costuras en la cara del material. Lo que es más agradable, la textura inusual de los bloques cuando se pliegan, e incluso durante la instalación, le permite hacer que la estructura sea perfecta.
- Aislamiento térmico y acústico. Gracias a su estratificación, las losas suprimen el ruido y retienen el calor dentro del local. Las propiedades de aislamiento acústico de los edificios ubicados en el centro de la ciudad son especialmente importantes.
- Fácil de instalar. Debido a la ligereza de las losas compuestas, no se aplica una gran carga a los cimientos del edificio. Y dada la resistencia de las placas, no es necesario utilizar piezas de refuerzo adicionales. Basta con aplicar una estructura de marco simplificada para una fachada de ventilación.
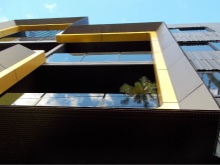
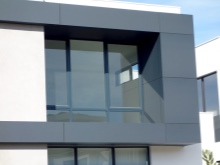
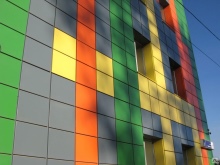
Alucobond también tiene algunas desventajas.
- Baja refractariedad. Por supuesto, este indicador está determinado por el tipo de relleno. Las placas, dentro de las cuales hay un polímero, no solo se queman, sino que también liberan sustancias tóxicas al aire. Es por eso que la mayoría de la gente opta por tableros con polietileno expandido, ya que pertenece a la clase de retardantes de llama. Hoy en día, el mercado de la construcción está lleno de paneles de alucobond con una composición interna mejorada. Contienen hidróxido de aluminio, que puede resistir el fuego abierto durante varias horas. Sin embargo, el precio de dicho material es mucho más elevado. En consecuencia, no se compran con tanta frecuencia.
- Restauración de forjados. Si el bloque se daña repentinamente, puede ser necesario desmontar varios bloques de losa adyacentes para reemplazarlo.
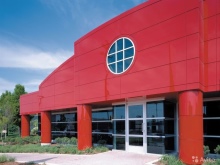
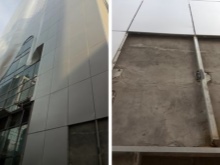
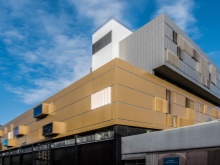
Aplicaciones
Alucobond es un material de construcción tan versátil que se utiliza en una amplia variedad de áreas de producción.
- Los paneles compuestos ocupan hoy el primer lugar entre los materiales destinados a la decoración de la fachada de los edificios.
- Alucobond se utiliza como fachada ventilada de edificios obsoletos para renovar el exterior y aumentar las propiedades de aislamiento acústico y térmico.
- Los sándwiches de bloque se utilizan como revestimiento para detalles arquitectónicos.
- Las placas de este tipo se utilizan en el diseño de carteles publicitarios, tableros de pie, cajas de luz.
- Los nuevos bloques se pueden utilizar para hacer tabiques dentro del local o para terminar el espacio interior, incluido el techo.
- Seguro que pocas personas lo saben, pero los paneles compuestos se utilizan para la fabricación de algunos elementos de acabado para automóviles, autobuses e incluso automóviles.
- Alucobond se utiliza como embalaje protector para equipos frágiles.
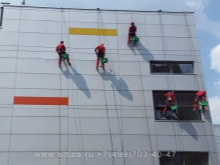
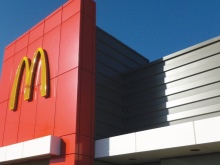
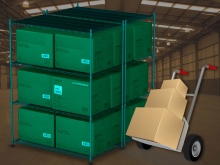
Los paneles compuestos de aluminio hacen su trabajo fácilmente. Sin embargo, se utilizan con mayor frecuencia como material de acabado para la parte frontal de edificios e interiores.
Son estos bloques los que le permiten crear obras maestras arquitectónicas únicas al organizar el exterior de un edificio.
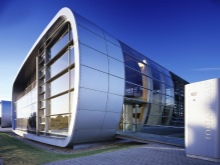

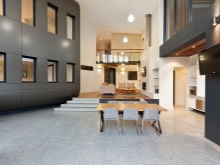
Descripción de especies
Hoy en día, existen varias variedades de paneles compuestos de aluminio, cada uno de los cuales tiene numerosas ventajas, pero puede tener algunas desventajas.
- Fachada ventilada con alucobond. La instalación es muy sencilla. Para la instalación, se utilizan sujetadores, en los que se instala inicialmente el aislamiento. A continuación, se unen las guías y el perfil, y luego se fijan los paneles. Gracias a este diseño, los edificios reciben la máxima protección contra daños mecánicos y, lo más importante, el calor se retiene dentro del edificio.
- Alucobond debajo de un árbol. Con la ayuda de tales losas, el edificio adquiere un aspecto inusual. Cada bloque individual está cubierto con pintura de alta calidad que no se agrieta con el tiempo, no pierde saturación y profundidad de color, así como la textura visible de la madera natural.
- Alukobond A2. Un rasgo distintivo de este tipo de panel es la incombustibilidad. Incluso con el calor fuerte de las llamas directas, la estufa no se encenderá. En consecuencia, tales placas están destinadas a su uso en edificios donde la cuestión de la seguridad contra incendios está en primer lugar.
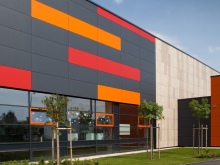
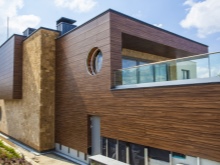
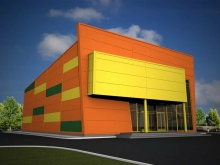
Cabe señalar que las placas compuestas de aluminio se fabrican con varias marcas.
El primero es B2. Tales placas no pueden soportar una llama abierta, por lo que pertenecen al cuarto grupo de inflamabilidad. No solo se encienden por el contacto con el fuego, sino que también se encienden rápidamente. Otra característica distintiva de los paneles compuestos de aluminio B2 es la mínima resistencia a la flexión.
La siguiente marca es A2. Estos modelos tienen un índice de inflamabilidad mínimo, que se indica con los símbolos "G1". Hay variedades de placas con la designación "NG". Esto sugiere que no son inflamables. En cuanto a las dimensiones de las placas marcadas con A2, son completamente idénticas a las del alucobond B2. La única diferencia está en la masa. Las placas A2 pesan 1,5 kg más que las placas B2.
Otro tipo de casetes compuestos es plus. Estos tableros se diferencian por el grosor máximo. El peso de cada unidad individual es de 7,3 kg. Los indicadores de inflamabilidad e inflamabilidad son mínimos.
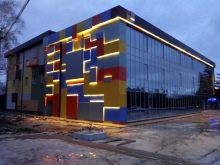
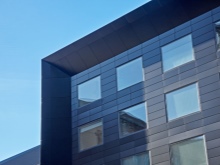
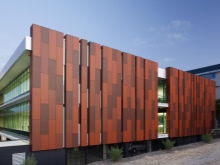
Dimensiones y peso de las hojas
Los paneles compuestos de aluminio con marcado plus tienen el ancho máximo posible: 1,5 m, y el ancho de los paneles compuestos con marcado B2 es de 1 m. La señalización Alucobond A2 tiene una anchura media de 1,25 m. Las mismas losas se pueden pedir con un ancho de metro y medio, ya que es casi imposible encontrar losas A2 más grandes que el ancho especificado a la venta.
No existe un estándar específico para la longitud de los bloques de alucobond. Este indicador dimensional varía de 2 a 4,5 m, sin embargo, al examinar las fachadas de los edificios terminados con alucobond, también se observan dimensiones atípicas de las losas. Esto se debe a algunos de los matices de la producción de bloques. Van a lo largo del transportador en una cinta continua y se cortan según la longitud requerida por el cliente.

Pero incluso en el caso de pedidos individuales, debe recordarse que no se pueden exceder las normas permitidas.
Por ejemplo, la longitud máxima de una losa puede ser de 6 m La longitud de cada bloque individual no debe exceder los 160 cm.
El grosor del alucobond es igualmente importante. Sin embargo, esta cifra depende del relleno del bocadillo. Según los fabricantes, la demanda de los consumidores se centra más en losas de 4 mm de espesor.
Vale la pena familiarizarse con la masa del alumabond. Por 1 metro cuadrado. m de este material representa de 3 a 8 kg. Todo depende de los materiales utilizados para componer los paneles compuestos.
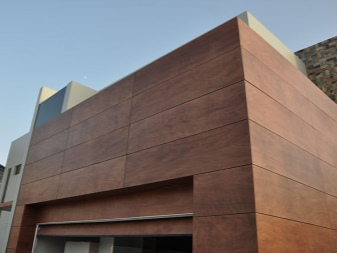
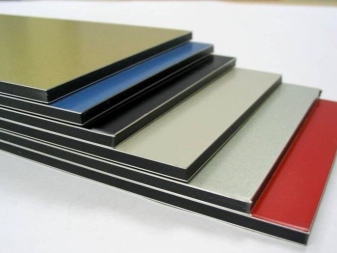
¿Cómo trabajar con paneles?
A las personas que nunca se han encontrado con este tipo de material les resulta muy difícil trabajar con él. Pero no es así. De hecho, los paneles compuestos de aluminio se pueden instalar sin siquiera un conocimiento mínimo de cómo hacerlo. Lo principal es comprender la tecnología de instalación y descubrir algunos de los matices de la instalación. En casa, las losas no solo se pueden cortar, sino que se pueden doblar solas para instalarlas en una superficie curva.
Con respecto al doblado de paneles de aluminio, se han desarrollado 3 métodos para este propósito.
- Prensa plegadora, que utiliza una automatización especializada diseñada para doblar láminas, placas, paneles y otros tipos de material.
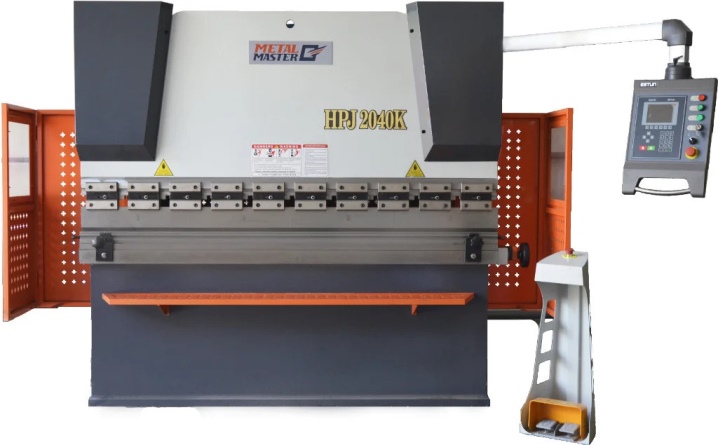
- Máquinas de laminado y curvado circular. En este caso, el proceso de deformación es algo similar a una plegadora. Sin embargo, se debe prestar especial atención a la protección de la parte frontal de los paneles.
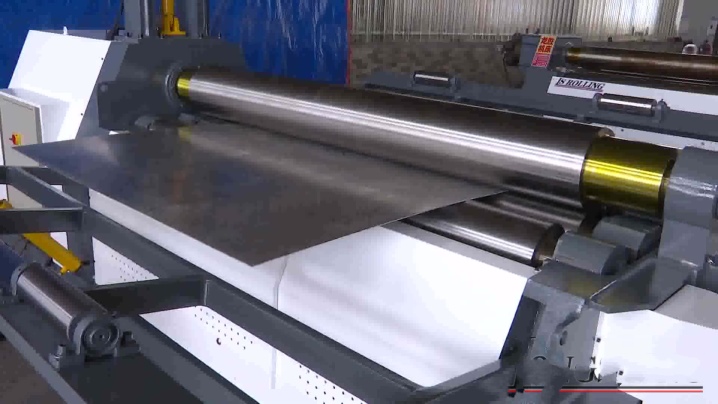
- Doblado manual por fresado. El fresado se realiza en la parte del panel donde se requiere curvar. Con cortadores, puede hacer cortes rectangulares o en forma de V. Estos cortes no deben extenderse al interior del panel por donde pasa el relleno. Después de preparar esta ranura, el doblado se lleva a cabo a mano hasta el radio requerido.
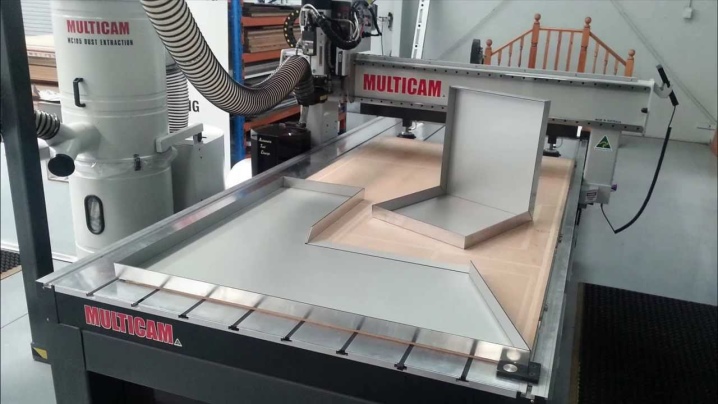
El tercer método es ideal para la tarea. Y lo que es más notable, en presencia de tales ranuras, las losas no pierden sus cualidades.
A la hora de cortar el tablero compuesto de aluminio, es necesario utilizar un cortador con tope guía. Pero si no existe tal herramienta, puede usar un molinillo. Solo cuando se trabaja con él, es importante tener especial cuidado y precaución, incluso una pequeña chispa puede tener consecuencias desagradables.
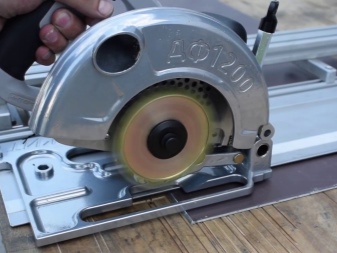
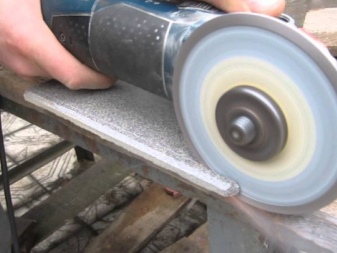
Tecnología de instalación
Personas ajenas a la industria de la construcción invitan a especialistas a montar el alucobond en la fachada del edificio. A los aficionados les parece que solo un profesional con una experiencia considerable en el montaje de placas compuestas puede hacer frente a este trabajo. Por supuesto, para la disposición de edificios de varios pisos, debe concluir un acuerdo con una empresa de construcción, pero al decorar la fachada de su propia casa, puede hacerlo usted mismo. Después de todo, no todo es tan complicado como parece a primera vista.
El Alucobond se fija al marco de metal mediante ensamblajes especiales. Los nodos de fijación en los que se deben sujetar las losas de revestimiento del edificio se dividen en varios tipos:
- suspendido sobre pernos;
- sujetado por ranuras y crestas;
- remachado
- atornillar
- adhesivo.
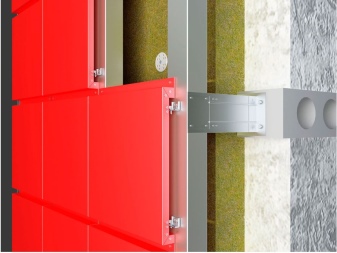
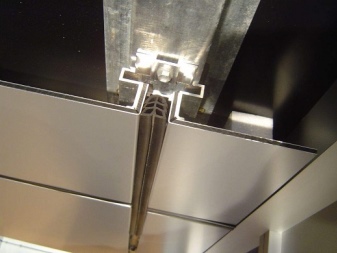
Cada opción individual garantiza una alta resistencia y confiabilidad de la fijación de las placas, lo principal es seguir la tecnología de instalación del perfil.
En general, el proceso de instalación consta de 3 etapas, la primera es la instalación del subsistema, la segunda es el aislamiento y la etapa final es la fijación de las placas.
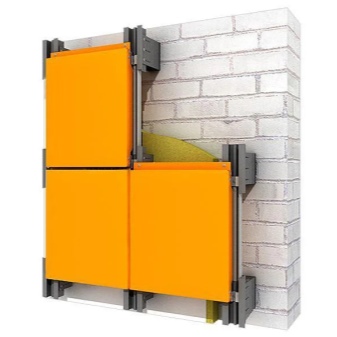
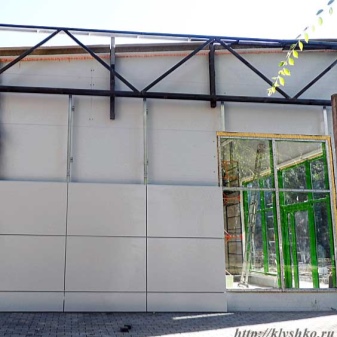
Instalación del subsistema
De acuerdo con la tecnología de instalación de alukobond, en primer lugar, es necesario hacer una marca de fachada. Para esto es necesario utilizar herramientas de alta precisión diseñadas para trabajar en lienzos grandes, por ejemplo, un láser o un teodolito. Si el edificio no es alto, es suficiente usar una cinta de construcción o una vara de medir.
La siguiente etapa de instalación es instalar los soportes. Con un taladro percutor, es necesario crear agujeros, cuyo diámetro debe coincidir con los pernos de anclaje. Y aquí hay un matiz importante: la profundidad del orificio debe ser 10 mm más que la longitud de los pernos.
A continuación, se instalan los soportes. Es sobre ellos que se llevará a cabo toda la carga de la fachada. En consecuencia, para que el revestimiento se asiente firmemente, es necesario instalar correctamente los soportes. Para empezar, se coloca una arandela de disco en un tornillo autorroscante. Luego, se insertan una junta de aislamiento térmico y una clavija de plástico en el orificio. Después de girar el tornillo.Este último en la instalación del subsistema implica la instalación de guías.
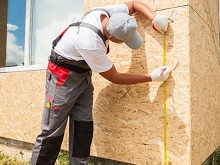
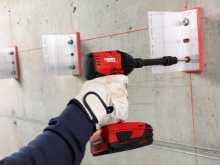
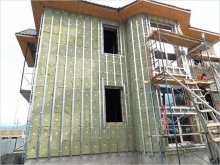
Calentamiento
Una etapa importante en la instalación de las placas es la colocación del aislamiento. La lana mineral más utilizada. También puede utilizar poliestireno o poliestireno expandido.
Las láminas de aislamiento están colgadas en soportes. Y para una mayor fijación, en algunos lugares se fijan con tacos.
En este caso, debe conocer un matiz importante: si se usa lana mineral, sus extremos deben estar cuidadosamente metidos debajo de los corchetes.
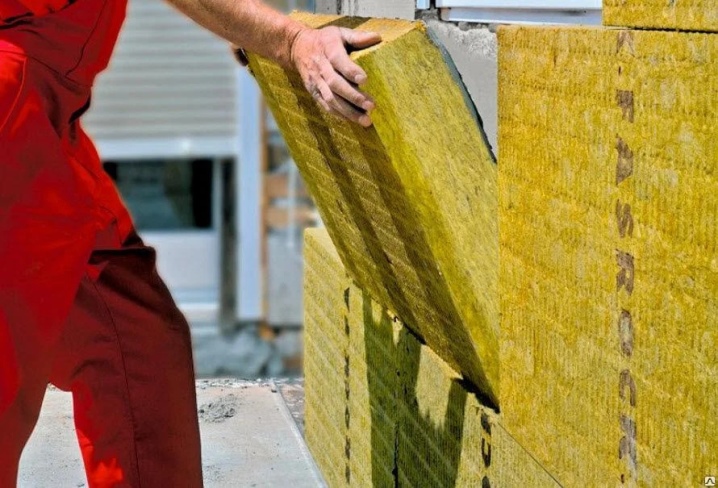
La etapa final
Y ahora solo queda instalar el alucobond en sí. La instalación de placas compuestas de aluminio se realiza según el tipo de sujetador. El más común, sin embargo, es con y sin candado. Los bloques deben instalarse de abajo hacia arriba, de izquierda a derecha. Con la ayuda de tornillos autorroscantes, la barra de inicio se fija. Para una conexión más estrecha, se recomienda colocar cinta de doble cara debajo de los casetes. Durante la instalación, es importante asegurarse de que el siguiente casete coincida con el anterior en las cerraduras.
Después de instalar cada placa nueva, se aprietan los tornillos. Si es necesario, se puede dejar un pequeño espacio entre los bloques. Los casetes que no tienen cerradura se instalan utilizando una tecnología similar mediante remaches.
Como se hizo claro la instalación del alucobond no es particularmente difícil. Por supuesto, para un principiante, instalar las primeras losas parecerá increíblemente difícil. Sin embargo, si se adhiere a todas las complejidades de la instalación, incluso una persona sin experiencia podrá equipar la fachada de su propia casa sin involucrar a especialistas en la industria de la construcción.
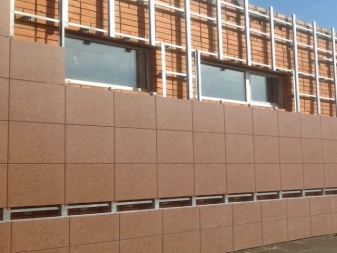
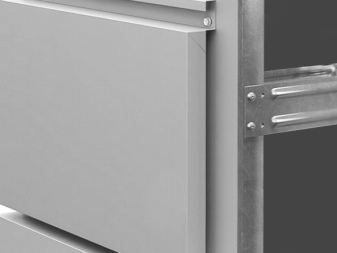
El comentario se envió con éxito.